Facility Managers are under pressure from every angle—rising energy costs, ESG mandates, aging infrastructure, and shifting occupant expectations. You’re expected to cut utility bills, extend equipment life, and meet sustainability goals—without compromising comfort or uptime.
But let’s face it: swapping in LED lights or tweaking thermostats isn’t enough anymore. Many facilities still lose thousands annually through outdated equipment, inefficient systems, and missed optimization opportunities. This translates to wasted resources and missed savings, but the consequences extend further: diminished asset value, increased compliance risks, and eroded stakeholder trust.
This guide isn’t about surface-level upgrades. Inside, you’ll discover high-impact best practices and cutting-edge technologies proven to deliver substantial consumption reductions, significant cost savings, and extended equipment lifespan. Whether you oversee a sprawling campus, a high-rise commercial building, or a complex industrial site, these energy-efficient strategies will future-proof your facility and transform sustainability into a decisive competitive advantage.
A Strategic Approach to Energy Efficiency
Before diving into specific strategies, developing a comprehensive energy management plan is crucial. This plan should outline your facility’s energy goals, identify areas of improvement, prioritize projects based on ROI, and establish a system for ongoing monitoring and optimization.
Key Elements of an Energy Management Plan:
- Energy Audit: Conduct a thorough assessment of your facility’s energy consumption to identify areas of inefficiency. This includes analyzing utility bills, inspecting equipment, and evaluating building systems.
- Benchmarking: Compare your facility’s energy performance against industry benchmarks and best practices to identify areas where you can improve. Tools like Energy Star Portfolio Manager can be valuable for this.
- Goal Setting: Establish specific, measurable, achievable, relevant, and time-bound (SMART) energy reduction goals.
- Prioritization: Prioritize energy efficiency projects based on their potential ROI, payback period, and alignment with your overall sustainability goals.
- Implementation: Develop a detailed plan for implementing energy efficiency projects, including timelines, budgets, and responsibilities.
- Monitoring and Verification: Track your progress towards your energy goals and verify the effectiveness of your energy efficiency projects. Use data analytics and reporting tools to monitor energy consumption, identify trends, and make adjustments as needed.
- Continuous Improvement: Regularly review and update your energy management plan to ensure it remains effective and aligned with your evolving needs and goals.
Quick-Win Energy Strategies for FMs
Here’s a prioritized overview of high-impact energy efficiency strategies:
Strategy | Investment Level | Avg. Savings | ROI Timeline |
HVAC System Optimization | Medium-High | 20–50% HVAC energy | 1–3 years |
Smart Lighting Controls | Low-Medium | 20–60% lighting energy | <2 years |
Building Automation Systems (BAS) | Medium-High | 10-30% overall energy | 2-5 years |
Variable Frequency Drives (VFDs) | Medium | 30–50% motor energy | <2 years |
Compressed Air Leak Detection | Low | 15–25% air system energy | Immediate |
Heat Recovery Ventilation (HRV) | Medium-High | 14–23% HVAC savings | 3 years |
Understanding the Energy Efficiency Reliability Curve
When planning energy upgrades, it’s easy to assume that savings scale linearly with investment. In reality, energy efficiency follows what’s known as the reliability curve—a concept that illustrates how early-stage improvements deliver the most significant returns, while later upgrades become increasingly expensive for smaller gains.
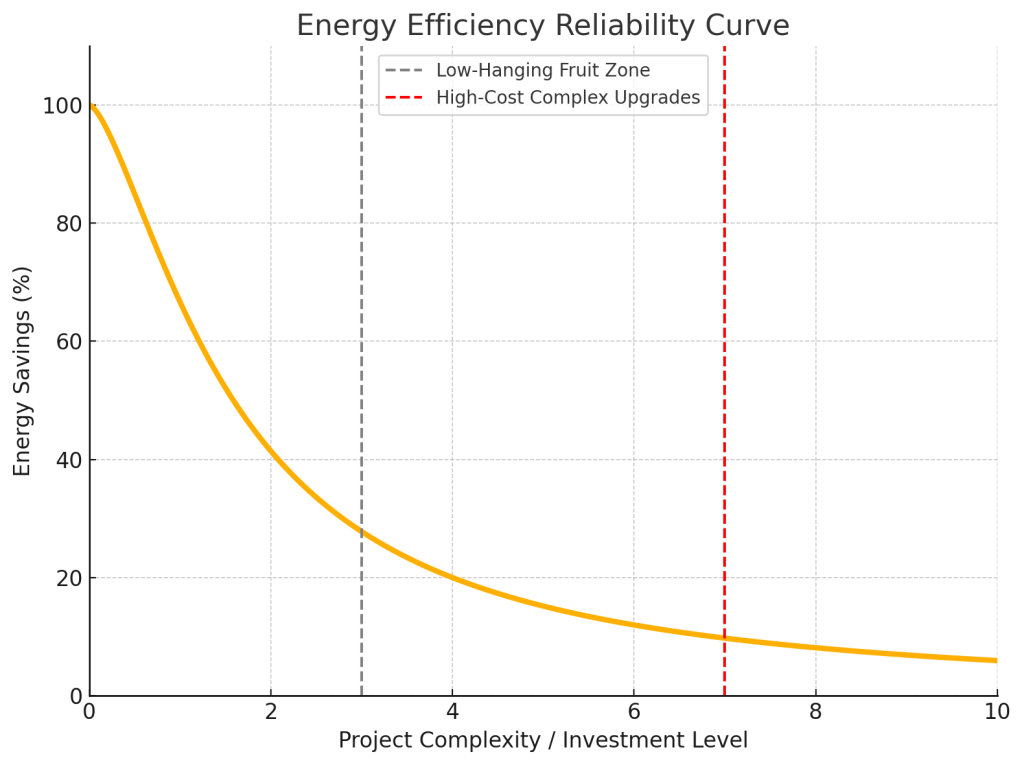
The Three Phases of Energy Efficiency ROI:
Low-Hanging Fruit (High ROI, Low Cost)
These are the foundational improvements that offer fast payback and minimal disruption.
- LED retrofits
- Occupancy-based controls
- Basic HVAC optimization
These typically yield 20–60% savings with a return on investment in less than two years.
Intermediate Upgrades (Medium ROI, Moderate Cost)
These projects require more coordination and capital, but still deliver strong results.
- Variable Frequency Drives (VFDs)
- Heat Recovery Ventilation (HRV)
- BMS or EMS upgrades
These strategies average 10–30% savings and often return value within 2–5 years.
Advanced Retrofits (Low ROI, High Cost)
As you push closer to net-zero performance, further savings become harder and more expensive to achieve.
- Deep insulation retrofits
- On-site renewables with storage
- Full HVAC replacement before end-of-life
At this stage, every additional percentage of energy saved comes at a steeper price and with diminishing returns.
Why it matters
Understanding the reliability curve helps facility managers prioritize projects that offer the most value first, maximizing energy reduction per dollar spent. It also sets realistic expectations about long-term planning and capital budgeting for deeper sustainability goals.
12 Energy Efficiency Strategies for Facilities
1. Maximize Lighting Efficiency with Smart Controls
While switching to LEDs is an important first step, realize the full potential of your lighting system with intelligent controls. By integrating:
- Dimmable LEDs with Daylight Harvesting
Optimize energy use by dynamically adjusting artificial light levels based on available natural light.
- Occupancy Sensors
Eliminate wasted energy by ensuring lights are active only in occupied spaces.
- Integrated Smart Lighting Systems
Connect lighting to your Building Management System (BMS) for centralized, automated control and enhanced energy optimization.
These advanced strategies go beyond basic energy reduction. The Department of Energy (DOE) estimated that adopting LED lighting would lead to 75% energy savings.
Utilize Advanced Lighting Concepts
- Circadian Lighting
Design lighting systems that mimic natural daylight patterns to support occupant health and well-being, improving productivity and reducing energy costs.
- Human-Centric Lighting (HCL)
Prioritize the biological effects of light on humans, considering factors like color temperature and intensity to optimize visual comfort, mood, and alertness.
2. Automate HVAC with Occupancy-Based Setback Controls
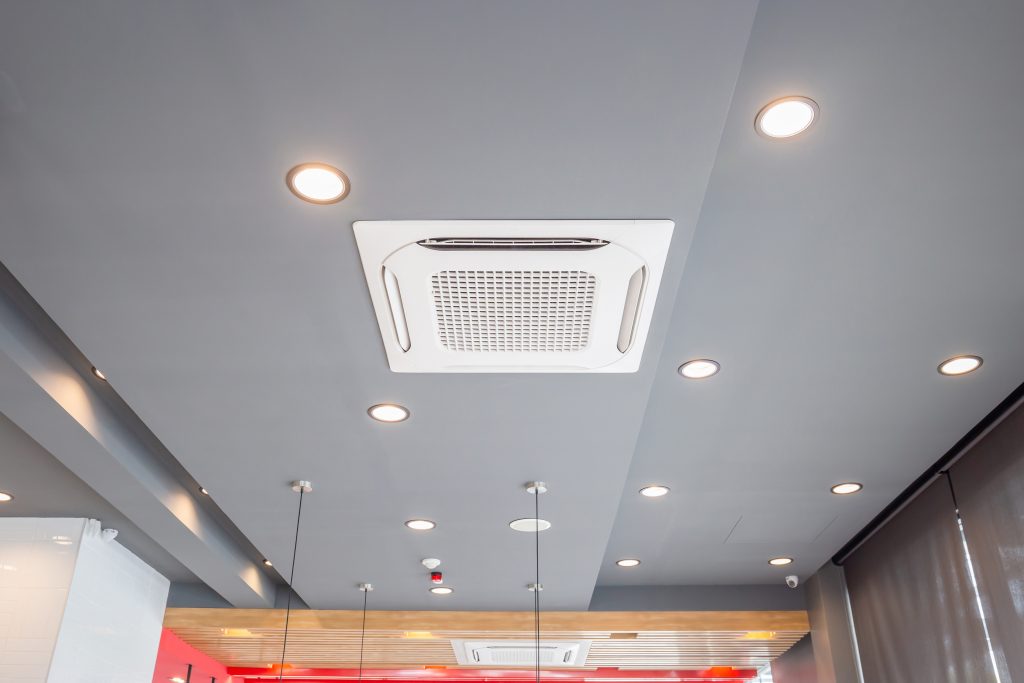
Optimize HVAC energy consumption by dynamically aligning system output with real-time occupancy.
To achieve this, integrate:
- Occupancy Sensors and Smart Thermostats
Enable precise, zone-specific temperature control based on presence, minimizing energy waste in unoccupied areas.
- BMS-Integrated Zoned HVAC
Leverage a Building Management System (BMS) to deliver granular, automated control of heating and cooling, which is particularly essential for maximizing efficiency in today’s flexible, hybrid work environments.
This strategy transcends basic temperature adjustments. Energy savings increase with lower occupancy and more extended unoccupied periods, ranging from 24.78% to 46.05% depending on building size (small to large) and unoccupied time (2 to 6 hours).
This proactive approach also extends equipment lifespan, lowers maintenance demands, and enhances overall system reliability, contributing to a more sustainable and cost-effective facility.
What is a Building Automation System (BAS)?
A BAS is a centralized control system that integrates and automates various building systems, including HVAC, lighting, and security. A well-designed BAS can optimize energy performance, improve occupant comfort, and streamline building operations.
Key features of a BAS include:
- Centralized control and monitoring
- Automated scheduling
- Fault detection and diagnostics
- Energy management and reporting
- Integration with other building systems
BAS optimization can reduce energy consumption in commercial buildings by approximately 29%.
3. Reduce Heat Loss with Automated Window Shades
Inefficient windows can significantly impact a building’s energy performance.
Consider these advanced window technologies:
- High-Performance Windows
Install double- or triple-pane windows with low-emissivity (low-E) coatings to minimize heat transfer.
Savings:
- Up to 40% less heat loss in winter
- Up to 60% less solar heat gain in summer
- Up to 15% reduction in annual HVAC demand
- Automated Shading Systems
Integrate motorized shades with sensors and controls to automatically adjust shade position based on sun angle and occupancy.
- Dynamic Glass
Use electrochromic glass that changes its tint in response to sunlight, reducing solar heat gain and glare.
4. Recover Heat with Energy-Efficient Ventilation Systems
Heat Recovery Ventilators (HRVs) reuse exhaust air to precondition incoming fresh air, reducing the load on your HVAC system.
- Summer savings up to 14.5%
- Industrial applications show 23% fuel savings and 18% energy cost reduction.
Energy Recovery Ventilators (ERVs)
In high-humidity environments, consider ERVs, which also transfer moisture between incoming and outgoing air, further improving energy efficiency and indoor air quality.
5. Capture Waste Heat from Hot Water Systems
Especially in facilities with high hot water demand (gyms, hotels, hospitals), hot wastewater can preheat incoming cold water, reducing boiler demand.
Here’s a clean diagram illustrating the Hot Water Heat Recovery Process:
Top row: Hot wastewater flows through a heat exchanger, transfers heat, and exits as cooler wastewater to the drain.
Bottom row: Cold incoming water absorbs the heat from the exchanger and moves forward as preheated water to the boiler/heater.
Capturing waste heat can yield 5–40% savings on water heating systems and complements existing sustainability initiatives.
6. Install Door Interlocks in Conditioned Docks and Bays
Heated or cooled loading docks often hemorrhage energy when doors remain open. Installing automatic door interlocks that shut off heating/cooling during open-door periods can yield major savings, especially in extreme climates.
7. Use Variable Speed Drives (VSDs) on Motors and Pumps
VSDs adjust motor speed based on load rather than running at full capacity, significantly reducing energy consumption.
Savings:
- 30–50% on HVAC, chilled water, and pump systems
- 1–2 year ROI
Variable Frequency Drives (VFDs)
A type of VSD that controls the frequency of the electrical power supplied to the motor, allowing for precise speed control and energy savings.
- VFDs can be used with various motor types, including induction motors and synchronous motors.
- When selecting VFDs, consider factors such as motor horsepower, voltage requirements, and application-specific needs.
- Proper installation and programming are essential for optimal VFD performance and energy savings.
8. Switch Belt-Drive Motors to Direct Drive
Direct drive systems eliminate belt friction and slippage, reducing energy waste and maintenance needs.
- Up to 20% energy savings
- Lower decibels (up to 9% quieter)
- Less wear = fewer breakdowns
9. Upgrade Fans with Advanced Aerodynamics
Newer fan blade designs and composite materials enable better airflow using less power. Many modern systems also support direct drive and smart integration.
Retrofits in return air systems or commercial exhaust fans often yield up to 30% energy efficiency gains.
10. Audit and Repair Compressed Air Leaks
Compressed air is one of the most energy-intensive systems in manufacturing. Leaks are invisible to the ear but devastating to your energy bill.
Best practice:
- Use ultrasonic leak detection tools to identify and quantify leaks. Many offer ROI calculators based on pressure and dBA signatures.
- Regular leak detection and repair can improve compressed air system efficiency by 15-25%.
11. Upgrade Aging Equipment Based on SEER Ratings
Your HVAC unit might still be functional, but is it efficient?
- Strategy:
- Compare current SEER (Seasonal Energy Efficiency Ratio) rating with new models.
- Run a 5- to 10-year lifecycle ROI to justify mid-life replacements.
- Studies show even partial HVAC replacements can reduce energy use by 25–35%.
Aligning with Global Sustainability Standards
Energy strategies should not only save costs—they should also support your organization’s broader compliance and ESG goals.
Certifications to Consider:
- LEED (Leadership in Energy and Environmental Design)
- ISO 50001 (Energy Management Systems)
- Energy Star Certification
Why It Matters
Projects aligned with these standards are more likely to qualify for tax incentives, attract ESG-conscious investors, and enhance your brand’s reputation for corporate responsibility.
12. Monitor, Benchmark, and Continuously Optimize
Post-installation optimization is where real savings stack up.
- Key Metrics to Monitor:
- Energy Use Intensity (EUI): kWh or BTU per square foot
- Mean Time Between Failures (MTBF) for critical equipment
- Energy Star score
- Maintenance costs per square foot
- Occupancy-based HVAC runtime
- Indoor Air Quality (IAQ) parameters (CO2, VOCs)
- Tools and Technologies:
- Energy Management Systems (EMS)
- Building Management Systems (BMS)
- IoT sensors and analytics platforms
- Computerized Maintenance Management Systems (CMMS)
- Regularly analyze data from these tools to identify trends, detect anomalies, and fine-tune system performance.
Integration of Advanced Technologies in Energy Management
Emerging technologies are transforming how facilities monitor, control, and optimize energy use.
- Internet of Things (IoT): IoT sensors collect real-time data on temperature, occupancy, and equipment status.
- Artificial Intelligence (AI): AI algorithms analyze IoT data to predict usage patterns, detect inefficiencies, and automate adjustments.
- Example: Smart HVAC systems integrated with IoT sensors and AI can automatically adjust airflow and temperature in response to occupancy changes, resulting in up to 30% energy savings without compromising comfort.
- Digital Twin Technology: Create virtual models of your facility to simulate different energy scenarios and optimize performance before implementing changes in the real world.
Engaging Stakeholders in Energy Efficiency
Effective energy management is a team sport. Involving employees, vendors, and building occupants in sustainability initiatives boosts adoption and impact.
Strategies to Engage Stakeholders:
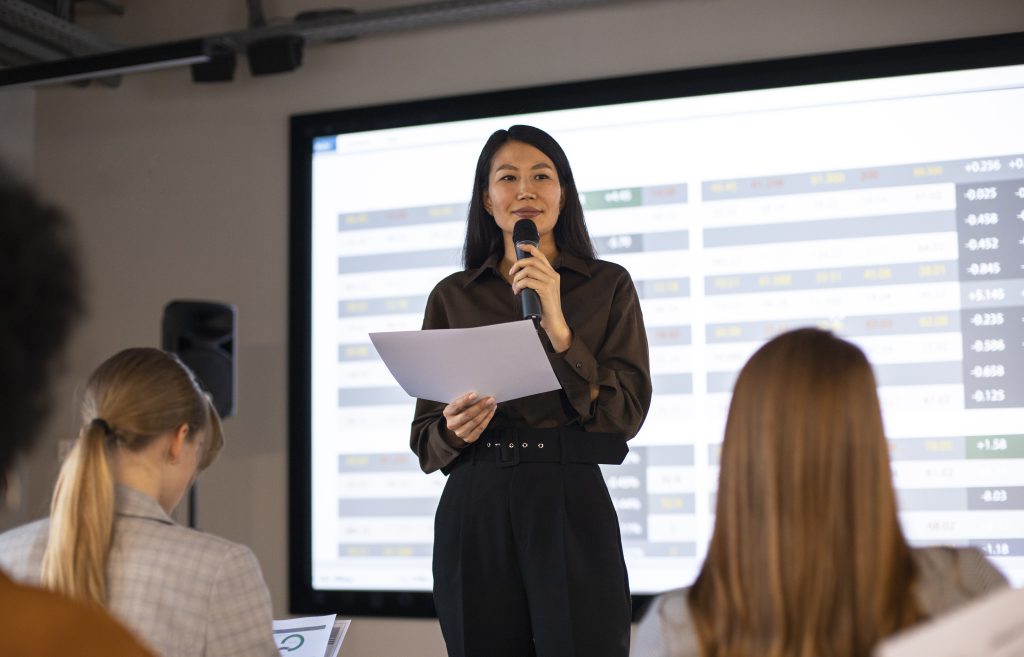
- Offer training on energy-saving protocols and smart system usage.
- Display real-time dashboards showing energy savings to motivate behavior change.
- Recognize and reward teams that meet energy reduction targets.
Why It Matters
Engaged stakeholders become energy champions, contributing to a culture of continuous improvement and accountability.
FAQs
How can a facility manager reduce energy costs quickly?
Start with occupancy-based lighting and HVAC controls—they offer fast ROI and minimal disruption.
What’s the ROI of LED upgrades?
Most LED retrofits pay for themselves in 12–24 months.
Is it worth upgrading HVAC before end-of-life?
Often, yes. New systems can cut operating costs by 20–30%, justifying early replacement.
Do green upgrades help with compliance?
Absolutely. Improvements often align with LEED, ISO 50001, and ESG mandates.
Final Thoughts
Energy efficiency isn’t just good stewardship—it’s smart business. When FMs take a strategic, ROI-driven approach, the results speak for themselves:
✅ Reduced utility bills
✅ Improved equipment reliability
✅ Lower emissions
✅ Healthier indoor environments
✅ Stronger stakeholder confidence
Partner With Left Coast Facilities Consulting
We help facilities like yours identify high-ROI savings opportunities through targeted audits, sensor upgrades, smart control retrofits, and more.
Ready to uncover hidden potential?
Contact us for a personalized energy performance assessment.